
در رویداد «ریورس پیچ» و پنلهای تخصصی در سومین نمایشگاه ملی فولاد مطرح شد؛
حمایت جدی فولاد مبارکه از افراد نوآور توانمند برای حل چالشهای صنعت
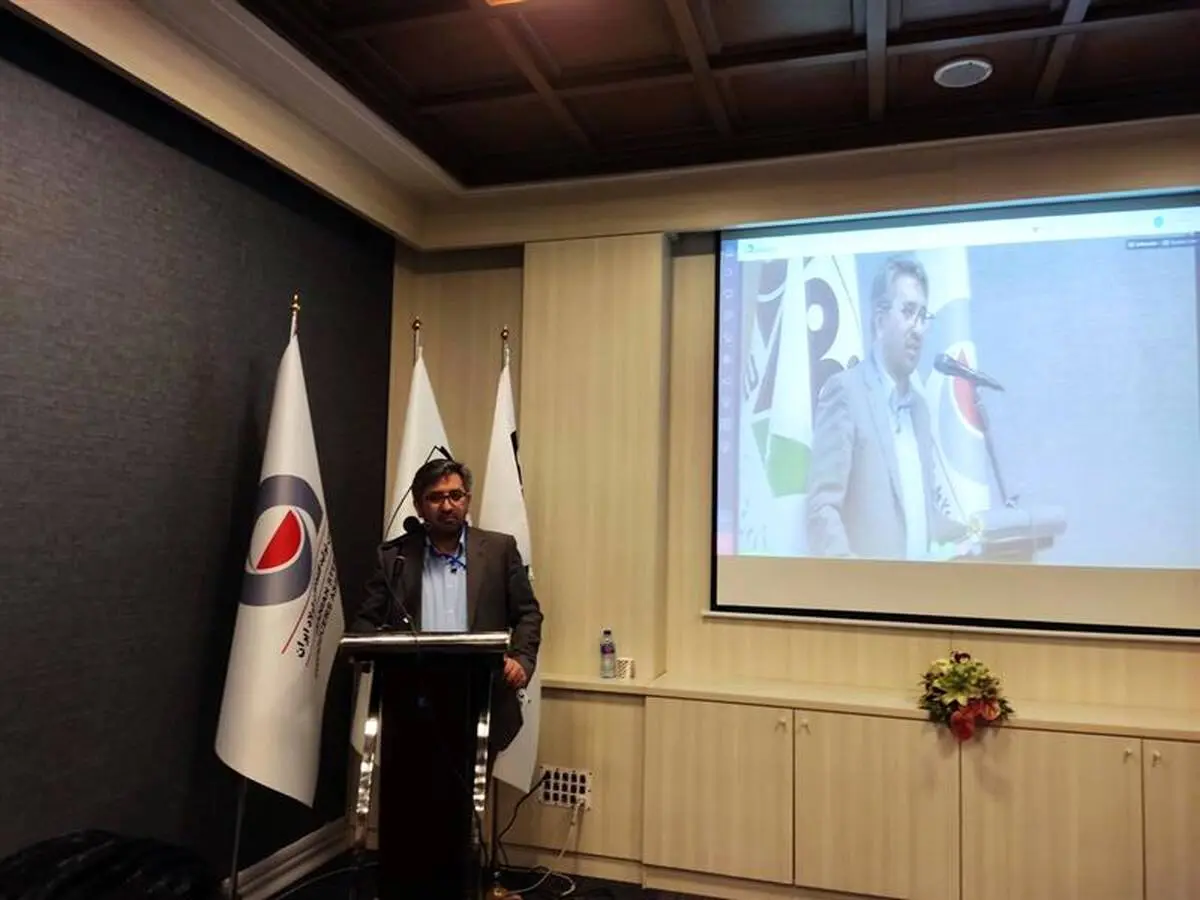
مدیرعامل شرکت پشتیبانی و توسعه فناوری و نوآوری فولاد مبارکه گفت: فولاد مبارکه میخواهد به افراد نوآور توانمند برای حل مسائل صنعت کمک کند تا راه حل خود را عملیاتی کنند. مهمترین بخش این فرآیند نیز تامین مالی این راه حلها است.
به گزارش شمانیوز، رویداد ریورس پیچ (Reverse pitch) به میزبانی شرکت فولاد مبارکه با محوریت رفع چالشهای صنعت توسط متخصصان در سومین نمایشگاه ملی فولاد ایران برگزار شد.
در این رویداد یحیی پالیزدار، مدیرعامل شرکت پشتیبانی و توسعه فناوری و نوآوری فولاد مبارکه، اظهار کرد: صنایع هم تامین کنندگان اصلی دارند و هم مشتریان که دو بال هر صنعت هستند. هرچه صنعت پیچیدهتر باشد صرفا نیاز به تامین تجهیز یا مواد اولیه نداریم بلکه به افرادی نیاز داریم که مسائل پیچیده ما را حل کنند. این مسائل پیچیده لزوما برای افراد خارج از صنعت آشکار نیست. یکی از ابزارهایی که میتواند این مسائل پیچیده را به سطح جامعه مخاطب یعنی افراد نوآور مرتبط وارد کند رویدادهای ریورس پیچ هستند.
برگزاری این رویدادها چند سالی است که در کشور رایج شده است و فولاد مبارکه نیز در همین راستا اولین رویداد از این نوع را در سال ۱۳۹۷ برگزار کرد. تفاوت رویداد امسال با سالهای گذشته این است که در سال جاری فولاد مبارکه صرفا از جامعه هدف خود راه حل نمیخواهد، بلکه میخواهد به آنها کمک کند تا راه حلها عملیاتی شود. مهمترین بخش این فرآیند نیز تامین مالی این راه حلها است که در نهایت میتواند بخشی از مشکلاتی که شرکتهای نوپا با آن مواجه هستند را حل کند.
تبدیل غبارات ناشی از حمل مواد و کورههای قوس به بریکت قابل شارژ
در ادامه ابراهیم روحاللهی به تبیین اولین چالش فولاد مبارکه با عنوان «تبدیل غبارات ناشی از حمل و شارژ مواد اولیه کورههای قوس الکتریک فولاد مبارکه به بریکت قابل شارژ با نوار نقاله» پرداخت.
وی اظهار کرد: در ناحیه آهن سازی فولاد مبارکه ابتدا کنسانتره به گندله تبدیل شده و سپس توسط ۸ مودول احیا به آهن اسفنجی تبدیل میشود. در مرحله بعد این آهن اسفنجی در ناحیه فولادسازی توسط ۸ کوره قوس الکتریکی و ۶ کوره پاتیلی به واحد ریختهگری مداوم ارسال شده و در نهایت از طریق ۵ ماشین دو خط به تختال تولید میشود. پس از این مرحله تختال تولید شده به ناحیه نورد گرم و سرد برای سایر فرایندها وارد میشود.
روحاللهی گفت: هنگام حمل مواد از ناحیه آهن سازی به فولادسازی توسط نوارهای نقاله و سپس از کورههای قوس الکتریکی غبارات ایجاد شده جمع آوری میشود که مقدار آن برای کورههای قوس ۱۱۰ هزار تن در سال و برای حمل مواد سالانه ۲۰ هزار تن غبار است. به همین دلیل فولاد مبارکه در تلاش است تا ضمن کاهش مقدار این غبارات، آنها را بازیابی و استفاده کند.
دومین چالش این رویداد به «ایجاد دانش فنی طراحی و تولید پودر قالب با توجه به پارامترهای ماشین ریختهگری و نوع محصولات تولیدی فولاد مبارکه» اختصاص داشت.
در این بخش منصور سنایی نژاد اظهار کرد: این چالش به قسمت ریختهگری مداوم مربوط میشود. در این قسمت پودر قالب به عنوان یک ماده مهم باعث ایجاد فولاد و افزایش کیفیت آن میشود. شرکت فولاد مبارکه به عنوان بزرگترین واحد فولادساز در کشور که از روش ریختهگری پیوسته پیروی میکند نیاز به بیش از ۴ هزار تن پودر قالب دارد.
راهکارهای مناسب برای کاهش پف و حجم سرباره کورههای قوس
سومین چالش رویداد ریورس پیچ فولاد مبارکه با عنوان «بررسی و ارائه راهکارهای مناسب برای کاهش پف و حجم سرباره در پاتیل حمل سرباره مربوط به کورههای قوس الکتریکی» توسط ابراهیم روحاللهی ارائه شد.
وی در این بخش از رویداد گفت: ورودی کورههای قوس الکتریکی عمدتا شامل مواد آهنی مثل قراضه، آهن اسفنجی و چدن است. افزودنیهای سرباره ساز آهک و دولومیت و متان و کک و... است. سرباره کمک زیادی در طی فرآیند میکند و قوس الکتریکی را پایدار، اتلاف حرارت، زمان ذوب و صدای قوس الکتریکی را کاهش میدهد. این سرباره پفکی با دو روش در فرآیند تولید میشود. اگرچه وجود این سرباره برای تولید مفید است اما زمانی که به پاتیل سرباره وارد میشود به دلیل محدودیت گنجایش با مشکل رو به رو میشویم؛ بنابراین باید آنها را جمع آوری کرد. در این مرحله نیاز به آنتی فومی است که بتواند پس از خروج از کوره و هنگام ورود به پاتیل سرباره، این پف را کاهش دهیم.
تلاش برای حذف پارگی ورق در کوره مافل
حمیدرضا شیخ در ارائه چالش چهارم با موضوع «طراحی، ساخت، نصب، راهاندازی، تضمین عملکرد و آموزش سیستم شناسایی عیب ویبره به منظور به صفر رساندن پارگی ورق در کوره مافل قلع اندود» اظهار کرد: خط قلع اندود یکی از خطوط تکمیلی در زنجیره ارزش افزوده فولاد مبارکه و هدف آن ایجاد لایه قلع روی ورق فولادی به منظور افزایش مقاومت نسبت به خوردگی شیمیایی است.
وی افزود: به دلیل وجود اختلافهای مقطعی و گذرا در طی فرآیند نورد، امکان وجود نوسان در ضخامت ورق وجود دارد که با عنوان «ویبره» شناخته میشود. این ویبره موجب تغییر مقطعی ضخامت ورق شده و در عرض آن دیده میشود. این تغییر در عبور از کوره باعث ذوب شدن و پارگی ورق در خط قلع اندود میشود و توقف اضطراری خط تولید را به دنبال دارد.
امکانسنجی افزایش توان خروجی نیروگاه بخار فولاد مبارکه
پنجمین چالش رویداد ریورس پیچ نیز به «امکان سنجی افزایش توان خروجی نیروگاه بخار فولاد مبارکه» اختصاص داشت. در این بخش محسن غلامی گفت: واحد انرژی و سیالات فولاد مبارکه وظیه تولید و تامین انرژی و سیالات را برای نواحی تولیدی بر عهده دارد و متشکل از چند واحد از جمله واحد نیروگاه است.
وی افزود: در این نیروگاه دو واحد دارد. نیروگاهی گازی با ظرفیت ۱۲۳.۴ مگاوات و راندمان ۳۲.۵ درصد است. نیروگاه بخار با ۳۴ واحد ۶۷ مگاوات ساعت با راندمان ۳۰ درصد است. المانهای اصلی آن از ۵ بویلر ۲۰۰ تن برای تولید بخار و ۳ توربین بخار با ظرفیت ۶۷ مگاوات است. چالش اینجا است که در سرویس قرار گرفتن همزمان هر ۳ واحد، واحد ۲ بخار به دلیل افزایش وکیوم برق کمتری تولید میکند و توان خروجی کاهش مییابد.
فرآیند پوستهزدایی EPS به عنوان جایگزین فرایند اسیدشویی
ششمین چالش این رویداد نیز به «فرآیند پوستهزدایی EPS به عنوان جایگزین فرایند اسیدشویی» اختصاص داشت. در این بخش میلاد وهمن، کارشناس مهندسی شرکت پشتیبانی و توسعه فناوری و نوآوری فولاد مبارکه، اظهار کرد: در ابتدای ناحیه نورد سرد، ورق فولادی در تماس با اکسیژن محیط دچار لایه اکسیدی در سطح خود میشود که این پوسته اکسیدی هم از نظر کیفیت ظاهری و انجام فرآیندهای بعدی برای ما مشکل ساز است. به همین دلیل رفع این پوسته اکسیدی یک الزام است.
وی افزود: به صورت معمول این لایه با فرآیند اسیدشویی از بین میرود و پس از آن ورق با آب شستشو میشود تا باقی مانده اسید روی سطح ورق از بین رفته و برای انجام سایر فرآیندها آماده شود. یکی از مشکلات این روش مصرف بالای آب و امکان تشکیل مجدد لایه اکسیدی به مرور زمان وجود دارد. بنابراین لازم است پس از اسیدشویی لایه نازکی از روغن بر سطح ورق پاشیده شود که این هم هزینهبر خواهد بود. این در حالی است که به دلیل خاصیت خورندگی اسید، برای استفاده از آن در برخی گریدهای فولادی محدودیت وجود دارد.
وهمن ادامه داد: امروزه فرآیند EPS به عنوان جایگزین اسیدشویی معمولی مطرح میشود که از سال ۲۰۰۸ تاکنون در شرکتهای فولادی مورد استفاده قرار میگیرد. در این فرآیند یک سلول EPS وجود دارد که مشابه مخازن اسیدشویی است. حجم این خط نیز یک دوم خط اسیدشویی متداوم است. به علاوه کیفیت پوستهزدایی در این روش بالاتر از روش اسیدشویی معمولی است و ۲۵ درصد هزینه تعمیرات کمتری دارد. همچنین از ضایعات این روش میتوان دوباره در چرخه تولید استفاده کرد.
هیدروژن سبز؛ فولاد سبز
چالش هفتم این رویداد نیز با عنوان «هیدروژن سبز؛ فولاد سبز» توسط سید شهاب حسینی، کارشناس مهندسی شرکت پشتیبانی و توسعه فناوری و نوآوری فولاد مبارکه مطرح شد.
وی در ارائه خود با اشاره به اهمیت فولاد سبز اظهار کرد: در روش تولید فولاد سبز واحدهای آهن سازی و احیا مستقیم درگیر هستند. کاهش تولید گازهای گلخانهای امروز یکی از چالشهای جهان است. با توجه به اثرات مخرب دی اکسید کربن سیاستهای بینالمللی برای کاهش تولید آن وضع شده است. در روشهای قدیمی به ازای تولید هر تن فولاد ۲ تن دی اکسید کربن تولید میشود.
حسینی ادامه داد: مقدار شدت انرژی از ۱۹ گیگاژول بر تن به ۱۶ گیگاژول بر تن و مقدار نشر گازهای گلخانهای از ۱.۴ تن به ازای هر تن فولاد باید به ۱.۱ تن تا سال ۲۰۵۰ کاهش یابد. فولاد سبز به کمک انرژی الکتریکی تجدیدپذیر و هیدروژن سبز تولید فولاد را از مبدا تولید عاری از گازهای گلخانهای میکند.
پنلهای تخصصی
گفتنی است علاوه بر رویداد ریورس پیچ، چند پنل تخصصی دیگر نیز در سومین نمایشگاه و جشنواره ملی فولاد به همت فولاد مبارکه برگزار شد که افراد حاضر در این پنل ها به ارائه مباحث تخصصی در حوزه صنعت فولاد پرداختند.
از جمله این پنلها میتوان به «بومیسازی صفحات مسی قالبهای ریخته گری» با ارائه سید مجتبی غیوری، «بومیسازی نمونهگیریهای اتوماتیک و تجهیزات آزمایشگاه گندله سازی» با ارائه نوید زندی و بنیامین یوسفی و ارائه پنل «پوشش دهی به روش پاشش حرارتی (HVOF) بر روی صفحات مسی قالبهای ریختهگری» از سوی روح الله بیرانوند و حمیدرضا سلیمی جزی اشاره کرد که هر سه در تالار مولوی هتل المپیک برگزار شد.
روابط عمومی شرکت فولاد مبارکه