
فولاد مبارکه/
تحول در انتقال سرباره کوره قوس الکتریکی شماره ۶ ناحیه فولادسازی و ریختهگری مداوم
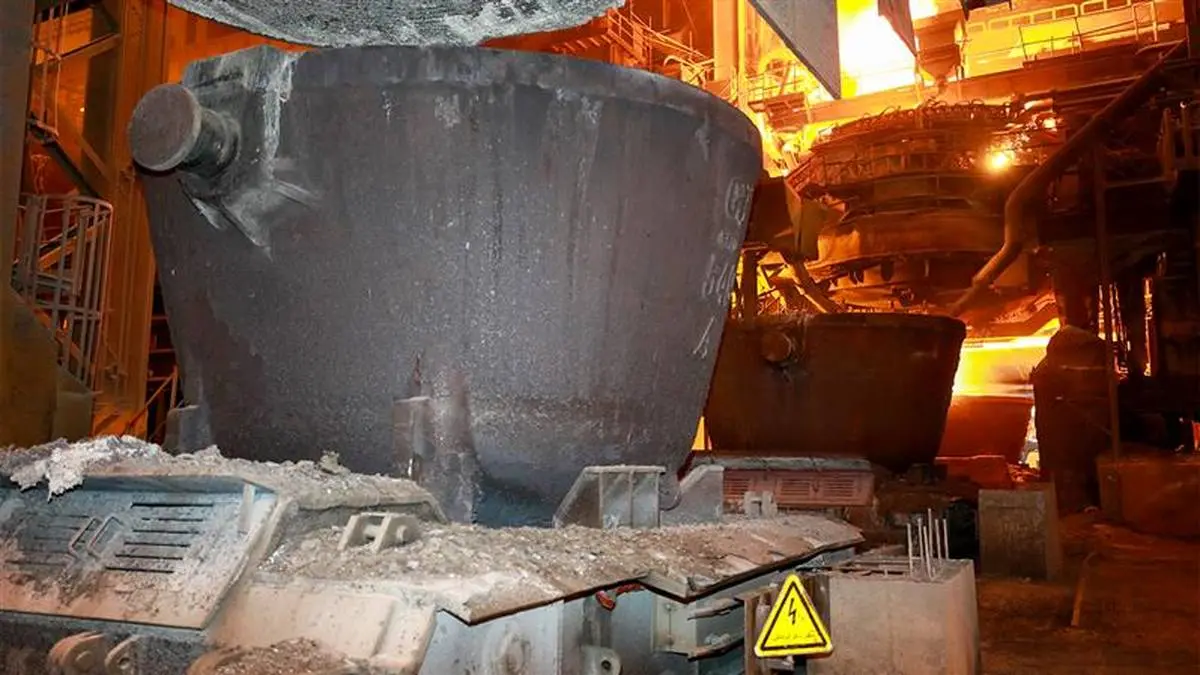
با اجرای پروژه نصب ریل و ارابه در کوره قوس شماره 6 در حمل پاتیل سرباره شرکت فولاد مبارکه، تحولی بزرگ انجام شد.
در روش قبلی پاتیل سرباره روی سکوی ثابت زیر کوره قوس قرار میگرفت و مکانیسمهای پاتیل بر تا زیر کوره حرکت میکردند و پاتیل پر را از زیر کوره انتقال میدادند و پاتیل خالی بعداً مجدداً روی سکو قرار میگرفت. این فرایند موجب ایجاد محدودیت در تزریق کربن و بعضاً سرریز شدن پاتیل سرباره میشد که با اجرای این پروژه دو پاتیل روی دو ارابه قرار میگیرد و با حرکت ارابه، حمل پاتیل ایمنتر میشود و محدودیت تزریق کربن به میزان زیادی کاهش مییابد.
در پی اجرای این پروژه موفقیتآمیز، خبرنگار فولاد طی مصاحبههای جداگانه، کم و کیف اجرا و اهمیت این پروژه را از برخی مدیران و مسئولان ناحیه فولادسازی و ریختهگری مداوم فولاد مبارکه جویا شده است که ماحصل آن را در ادامه میخوانید. با ما همراه باشید.
امیرحسین مرادی، رئیس تولید کورههای قوس الکتریکی
با اتکا به توان داخلی، پروژه کاملاً ایرانی راهاندازی و در خط سرویس قرار گرفت
بهینهسازی خطوط تولید بهمنظور افزایش کارایی تجهیزات، افزایش تولید، کاهش زمان صرفشده و کاهش انرژی از مهمترین اهداف مدیریت و کارکنان ناحیه فولادسازی است. در همین راستا، غلبه بر اصلیترین محدودیتهای تولید فولاد در قسمت کورههای قوس، یعنی تخلیه سرباره ذوب و بهینهسازی آن و کاهش خسارات ناشی از روش فعلی تخلیه سرباره که موارد ایمنی را نیز شامل میگردد در اولویتهای این ناحیه قرار گرفت. پس از تشکیل کارگروه مربوطه با مشارکت تولید و تعمیرات و دفاتر فنی تولید و تعمیرات و خدمات فنی ناحیه و همکاری قسمت جرثقیلهای فولادسازی جلسات متعددی برگزار شد و طرحها و ایدههای مختلف بررسی و سرانجام طرح استفاده از ۳ عدد ترانسفرکار انتخاب گردید و پس از شبیهسازی طرح و محاسبات نیروها و فرایندهای آن و تهیه نقشه، کلیه تجهیزات موردنیاز توسط تعمیرگاه مرکزی ساخته و تجهیزات غیرساختی خریداری و روی کوره ۶ نصب شد. در نهایت پروژه با توان داخلی و بهصورت کاملاً ایرانی راهاندازی شد و در خط سرویس قرار گرفت و هماکنون با موفقیت در حال بهرهبرداری است.
مجید دادجو، رئیس خدمات پشتیبانی ناحیه فولادسازی و ریختهگری مداوم:
در روش جدید، سرباره کوره از طریق 3 پاتیل سرباره که بر روی سه ترانسفرکار مستقرند به بیرون منتقل میشود
هماکنون بهمنظور جمعآوری سرباره ایجادشده در فرایند تولید فولاد در ناحیه فولادسازی از پاتیلهای سرباره 30 مترمکعبی استفاده میشود. الزامات فرایند تولید بهگونهای است که بهمنظور پفکی شدن بیشتر سرباره نیاز به حجم بیشتری از ظروف جمعآوری سرباره است.
پفکی شدن بیشتر سرباره سبب افزایش راندمان کوره، کاهش مصارف نسوز، انرژی، الکترود و پانلهای آبگرد میشود. در روش جدید، سرباره کوره از طریق 3 پاتیل سرباره که بر روی سه ترانسفرکار مستقر هستند به بیرون منتقل میشود. بنابراین حجم سرباره میتواند در یک ذوب به 90 مترمکعب یعنی سه برابر قبل افزایش یابد. ترانسفرکارها از طریق انرژی الکتریکی باتریها و با استفاده از اینورتر حرکت میکنند و باتریها در ایستگاههای معین شارژ میشوند. با توجه به خشن و گرم بودن محیط، برای انتقال انرژی الکتریکی به ترانسفرکارها از مکانیسمهای کابل و کابلجمعکن استفاده نشده و جهت انتقال فرمان از اتاق کنترل به ترانسفرکار از تجهیزات بیسیم صنعتی بهره گرفته شده است.
بهکارگیری این روش علاوهبر امکان افزایش حجم سرباره از سرریز پاتیل سرباره جلوگیری میکند که نهایتاً موجب کاهش زمان تخلیه ذوب و همچنین کاهش استهلاک مکانیسم حمل سرباره میشود. همچنین با حذف و یا کاهش سرریز سرباره، ریسکهای ایمنی مربوطه و آسیبهای انسانی و تجهیزاتی نیز رفع میگردد. این پروژه با بهکارگیری حداکثر امکانات موجود و مشارکت تیم خدمات فنی ناحیه فولادسازی و همکاران دیگر قسمتها و همچنین شرکت احیا فرایند اجرا شده و از زحمات تمام همکاران قدردانی میکنم.
رحیم خلقی، رئیس واحد حمل و فراوری سرباره:
واحد حمل سرباره همراستا با تغییر فرایندها، پیگیر و مصمم در تحقق طرحهای تولید
به فضل الهی و تلاش و کوشش کارکنان خدوم واحد حمل و فراوری سرباره و واحدهای تولید، اجرای پروژه ارائه سرویس بهموقع و مطلوب حمل سرباره کوره قوس الکتریکی شماره 6 مدنظر ناحیه فولادسازی انجام گرفت و همچنین پس از ارزیابی و بررسی نقاط قوت و ضعف پروژه، اصلاحات موردنیاز در جهت تحقق اهداف سازمان در تولید محصولات کیفی توسط تیم کارشناسی صورت پذیرفت. واحد حمل سرباره همراستا با تغییر فرایندها خود را ملزم به اصلاح زیرساختی و تأمین کمبودهای تجهیزاتی و نیروی انسانی دانسته و بهطور مصمم پیگیر تحقق طرحهای تولید است. در پایان از مشارکت همکاران واحد سرباره در اجرای پروژههای نوآورانه و انجام وظایف قدردانی میکنم.
حمیدرضا شاکری، سرپرست تعمیرات جرثقیلها و ترانسفرکارهای فولادسازی:
استفاده از سه دستگاه ترانسفرکار برای به حداقل رساندن زمان توقفهای ناخواسته
افزایش بهرهوری تجهیزات همواره یکی از دغدغههای سازمانها برای افزایش میزان تولید و نهایتاً سودآوری شرکت است و شرکت فولاد مبارکه نیز از این قاعده مستثنا نیست و در کنار طرحهای توسعه همواره در حال تلاش برای افزایش بهرهوری تجهیزات موجود خود بوده است. یکی از محدودیتهایی که باعث کاهش راندمان و توقف کورههای قوس الکتریکی میگردد نیاز به کنترل حجم سرباره تولیدی به دلیل نوع تخلیه (داخل پاتیل) و انتقال سربارهها (حمل توسط پاتیل بر) است. بر همین اساس پروژهای با محوریت مدیریت وقت ناحیه (مهندس سلیمی) تعریف و در دستور کار قرار گرفت که بر اساس آن با استفاده از 3 دستگاه ترانسفرکار بتوان با حداقل زمان توقف ممکن، پاتیل سرباره را در موقعیت دریچه تخلیه قرارداد تا عملاً زمان توقف ناشی از تعویض پاتیل توسط ماشینهای حمل سرباره را حذف کرد.
با توجه به اینکه نیاز بود این پروژه با حداقل هزینه و حداقل زمان ممکن اجرایی گردد، استفاده از ترانسفرکارهای قدیم حمل سبد قراضه که از مدار تولید خارج شده بودند در دستور کار قرار گرفت که نهایتاً با همکاری واحدهای خدمات فنی ناحیه، تعمیرگاه مرکزی، دفتر فنی تعمیرات 07 و همکاران واحد تعمیرات جرثقیلها و ترانسفرکارهای فولادسازی با اعمال تغییرات بر روی سازه این تجهیزات، امکان نصب بر روی ریل ترانسفرکار کوره و همچنین قرار دادن پاتیل سرباره بر روی این تجهیز فراهم گردید.
از دیگر چالشهایی که از ابتدا بهشدت امکان اجرای این طرح را تهدید میکرد نحوه برقرسانی به این تجهیز به دلیل شرایط بسیار سخت محیطی بود که با همت کارشناسان و طراحان، راهحلی برای این مهم ارائه شد و نهایتاً پروژه با اراده و تلاش عوامل درگیر و با استفاده از توقفات کورهها در زمان محدودیت انرژی، طی چند مرحله بر روی کوره شماره 6 انجام شد و در بهمنماه 1401 به بهرهبرداری رسید.
در پایان از تلاش و همت همکاران واحد تعمیرات جرثقیلها و ترانسفرکارهای فولادسازی و همچنین پیمانکار این واحد که از طراحی تا ساخت، نصب و راهاندازی این پروژه تلاش کردند، تشکر و قدردانی میکنم.