
مدیر بخش نگهداری و تعمیرات :
نگاهی به نقش نگهداری و تعمیرات در بهره وری
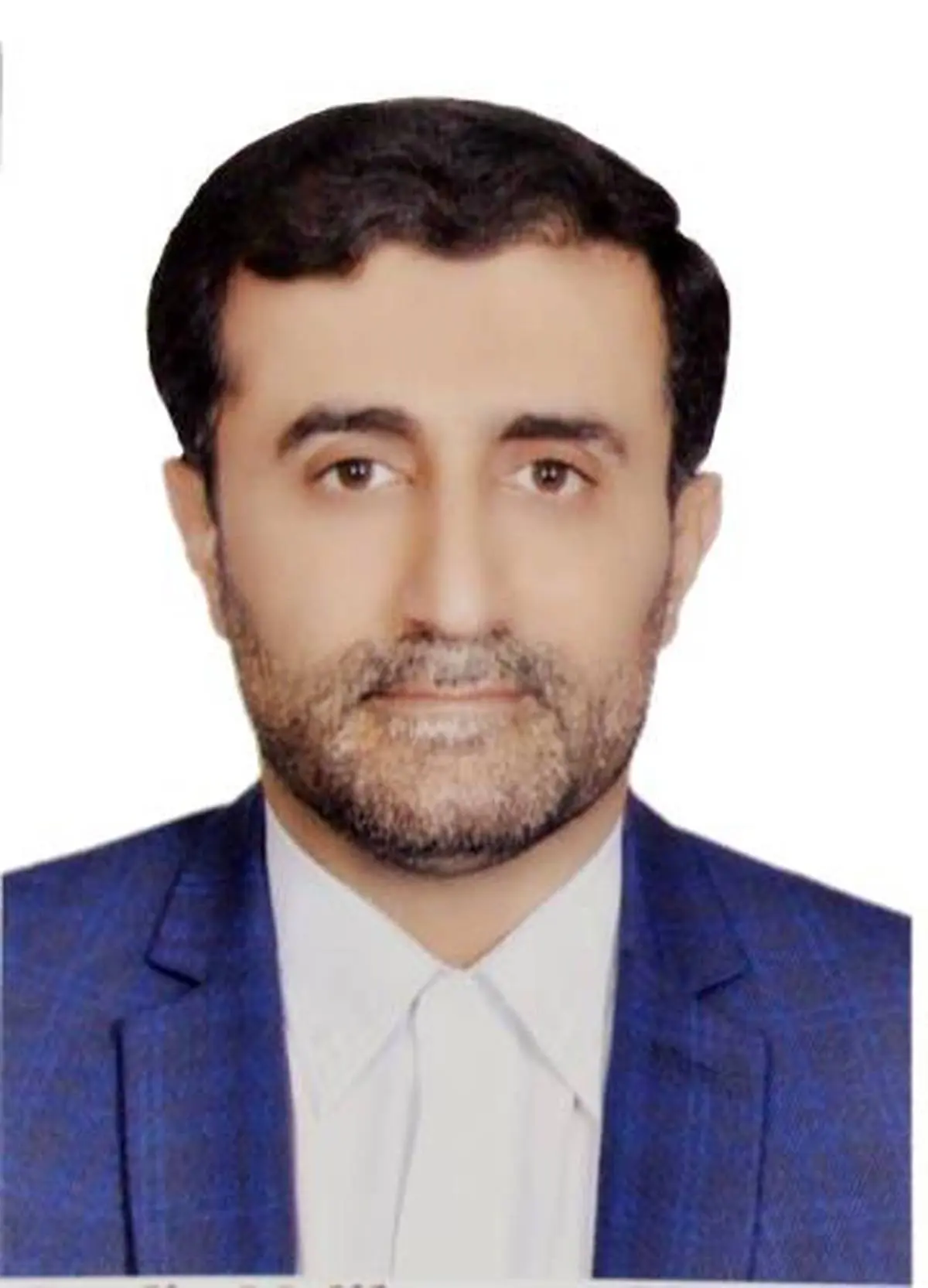
نگهداری و تعمیرات در فولاد خوزستان با استفاده از روشهای متداول و نوین و بهصورت نیمهمتمرکز انجام میشود، به این معنی که بخشی از آن در تیمهای مستقر در واحدهای بهره برداری و قسمتی که عمدتا شکل تخصصی در زمینه های برق، اتوماسیون صنعتی و ابزار دقیق، سازه های صنعتی و تعمیر تجهیزات مکانیکی دارند بهوسیله واحدهای پشتیبانی صورت می گیرد.
به گزارش خبرنگار شمانیوز و به نقل از روابط عمومی فولاد خوزستان: نظام نگهداری و تعمیرات شرکتهای فولادی بر مبنای تدوین اطلاعاتپایه، برنامهریزی، اجرا، نظارت، کنترل نگهداری و تعمیرات و درنهایت تهیه یا طراحی نرمافزار متناسب با شرایط سازمان است. شرکت فولاد خوزستان با توجه به برخورداری از نیروی انسانی متخصص و همکاری شرکتهای پیشرو در این زمینه، با طراحی و راهاندازی سیستم MIS بهعنوان یک CMMS (سیستم رایانهای مدیریت نگهداری و تعمیرات) نسبتا کامل اقدام کرده است. نگهداری و تعمیرات در این شرکت به روشهای زیر انجام میشود:
PM: تعمیرات پیشگیرانه در بخشهای الکتریکی، مکانیکی و ابزار دقیق، به دو روش روتین (A، B و C) و غیر روتین (در خصوص تجهیزات سایشی و مصرفی) انجام میشود.
CM: تعمیرات بر اساس پایش وضعیت که برای تجهیزات حساس و نیمهحساس مانند کمپرسورها، فنها، گیربکسها و ترانسفورماتورها اجرا میشود. در این شیوه لزوما به تعویض قطعات و تجهیزات بهصورت روتین نیاز نیست.
EM: درصورتیکه باوجود اعمال تمام برنامههای مذکور تجهیزی متوقف شد، بهصورت اضطراری رسیدگیهای مربوطه اعمال میشود.
میزان حساسیت در عملیات تعمیر و نگهداری
بهصورت کلی تجهیزات به سه بخش خیلی حساس، حساس و غیرحساس تقسیم شدهاند. فارغ از اینکه تجهیز در کدام بخش قرار دارد، بر اساس عملکرد آن، تکنیک نت متناسب با آن طراحی شده است. با برنامهریزی و هماهنگی در اجرای نت تجهیزات و نیمهمتمرکز بودن واحدهای نت، از انجام فعالیت جزیرهای و نامتوازن جلوگیری شده است. اجرای نیمهمتمرکز به این معنی است که بخشی از آن در تیمهای مستقر در واحدهای بهرهبرداری و قسمتی که عمدتا شکل تخصصی در زمینههای برق، اتوماسیون صنعتی و ابزار دقیق، سازههای صنعتی و تعمیر تجهیزات مکانیکی دارند بهوسیله واحدهای پشتیبانی صورت میگیرد.
پارامترهای موثر بر تعمیر و نگهداری
با استفاده از اسناد و اطلاعات فنی، شناسنامه تجهیزات و نیز نظر خبرگان فولاد، دورههای زمانی متناسب استخراج میشود. پارامترهای موثر بر آنها شامل زمان بین دو خرابی، آنالیز بازرسیها، تحلیل و ریشهیابی توقفهای رخداده و کیفیت قطعات خریداری شده است.
استفاده از نتهای متناسب با شرایط
ابزار و دانش موجود، کمک میکند تا تاکتیکهای نگهداری و تعمیرات را در جای مناسب خود استفاده کند. شایانذکر است که تجهیزات حساس شناسایی و همراه با اطلاعات فنی آنها در سیستم ثبت شدهاند و گروههای CM و بازرسان فنی به آنها اختصاص داده شدهاند. این گروهها بر اساس دورههای تعریفشده، با نمونهگیری یا دادهبرداری (شامل روغن، ارتعاش و ترموگرافی) از تجهیزاتی که بالغبر 1600 دستگاه هستند و تحلیل آنها، در صورت لزوم اقدامات اصلاحی انجام میدهند. نمودار «1» بیانگر درصد تحقق نت پیشبینانه است.
در خصوص تعمیرات اساسی و پیشگیرانه نیز در ابتدای هر سال اقدام به تهیه و تنظیم برنامههای تعمیراتی میشود. این برنامهها اعم از تعمیرات پیشگیری، اساسی و بازرسی، بر اساس استانداردهای تعمیراتی برای ماشینآلات، تجهیزات و ساختمانها تدوین میشود. در گام بعدی کنترل و هماهنگی برنامههای تعمیراتی با برنامه تولید واحدهای بهرهبرداری بهگونهای صورت میگیرد که زمان آمادهبهکار بودن تجهیزات با برنامههای تولید مطابقت داشته باشد. برای تضمین بازدهی حداکثر ماشینآلات و خطوط تولید با صرف حداقل هزینه، کمیت و کیفیت فعالیتهای تعمیراتی پایش شده و اقدامات اصلاحی در حدود تعیینشده، صورت میپذیرد. کنترل و بررسی کارآیی برنامههای تعمیراتی، فعالیتهای انجامشده در آغاز تعمیرات، حین توقف و پس از پایان تعمیرات، مورد تجزیهوتحلیل قرار میگیرد و با همکاری متخصصان واحدها انحراف از برنامهها پایش و اصلاح میشود. درنهایت با تهیه و جمعبندی گزارشهای ادواری از نتایج کارهای تعمیراتی و توسعه سیستمهای اطلاعاتی، آماده تهیه و تنظیم برنامههای سال آتی خواهیم بود.
اثر انجام فرآیندهای تعمیر و نگهداری دورهای بر راندمان تجهیزات
با پیشرفت روش نگهداری و تعمیرات از سال 1950 تاکنون و نیز انجام روشهای جدید بهصورت جزئی یا کلی، راندمان عملکردی تجهیزات در خطوط تولید بهبود یافت و منجر به این شد که در بازههای زمانی مختلف این عدد مورد تحلیل واقع شود. بهعنوانمثال در سالهای ابتدایی راهاندازی شرکت با توجه به نبود سیستمهای نت، میزان توقفات بسیار بالا بوده و پس از راهاندازی نت بر اساس دوره تناوب، کاهش توقفات بالایی به دست آمده است. با تکمیل سیستمهای نت این روند و راندمان عملیاتی طی چندین سال، روند مثبتی داشته است. نمودار «2» نمایانگر این روند در سالهای 1394 تا 1397 است.
محدودیتهای موجود در فرآیند تعمیر و نگهداری
در سازمانهای بزرگ صنعتی پیادهسازی و اجرای چرخه نگهداری و تعمیرات بسیار کلیدی و مهم و نیز بسیار سخت و زمانبر است. برای رفع این مشکل در واحد برنامهریزی تمامی محدودیتها استخراج، بازبینی و بهصورت بهینه هماهنگ شدهاند. نیروی انسانی بهطور مستمر تحت پایش قرار دارد و مسائل به واحد سازماندهی و روشها منتقل میشوند. در بخش تامین قطعات و تجهیزات با تقویت واحدهای ساخت و سفارشها، انجام بومیسازی و کنترل دقیق بر کیفیت تجهیزات و قطعات تامین شده، بخش زیادی از مشکلات رفع شده است. همچنین با نظارت و بازرسی فنی دقیق و سیستماتیک تجهیزات، ارائه بازخورد به واحدهای مرتبط و پیگیری اجرای آنها، اقدامات بسیار مطلوبی جهت بهبود محدودیتها در فرآیند نت حاصل شده است.
پیشرو در نظامهای نت
فولاد خوزستان جزو پیشروان نظامهای نت در سطح کشور است. با توجه به عملکرد تجهیزات، از سیستمهای EM (تعمیر بعد از خرابی)، PM (نگهداری و تعمیرات پیشگیرانه)، CM (پایش وضعیت تجهیزات)، TPM (نگهداری و تعمیرات بهرهور فراگیر) وRCM (نت مبتنی بر قابلیت اطمینان) در کمیتههای کاهش توقفات مورداستفاده قرار میگیرد. از نمونه فعالیتهای صورت گرفته RCM در بخش فولادسازی، پانلهای آبگرد کورهها است که با انجام فعالیتهای اصلاحی روی آن، توقفات حدود 30 درصد کاهش یافت و با تثبیت اقدامات، روند بهینه توقفات را طی سالیان بعدی داشتهایم. نمودار 3 بیانگر این موضوع است.
استانداردهای کار در شرایط اضطراری
توقفات در واحدهای تولیدی به دودسته برنامهای و اضطراری تقسیم شدهاند. در بخش توقفات برنامهای به لحاظ اینکه از قبل مشخصشده که در چه زمانیهایی فعالیت تعمیراتی نیاز است، تمامی فعالیتها با جزییات کامل شامل تعداد نیروهای انسانی با تخصص مربوطه، قطعات یدکی و مصرفی و روش انجام کار مورد ارزیابی قرار میگیرد. این ارزیابی از دیدگاههای ایمنی، فنی و تداخل کارها در جلسات مختلف بررسی و درنهایت زمانبندی و مسیر بحرانی پروژه مشخص میشود. در زمان اجرا، فعالیتها بهطور مستمر تحت پایش و پیگیری قرار گرفته و در هر زمان نیاز باشد، بههنگامسازی فعالیتها بهگونهای انجام میشود که تعمیرات با بهترین کیفیت و زمان بهینه به اتمام برسد.
در بخش توقفات اضطراری نیز تدوین و طراحی «استانداردهای کار در شرایط اضطراری» شامل شرح جزییات کار و تمامی اقدامات لازم جهت رفع اشکال مشخص شده و در اختیار بهرهبردار قرار گرفته است. در خصوص موارد ایمنی، سناریوها با توجه به شرایط خاص فعالیت/ موقعیت (مثلا کار در شرایط اضطراری و ...) نوشتهشده و مانورهای ایمنی بهصورت دورهای برگزار میشود.