
برای نخستین بار در کشور انجام شد؛
بومیسازی ضخامتسنج دیجیتال اشعه ایکس در فولاد مبارکه
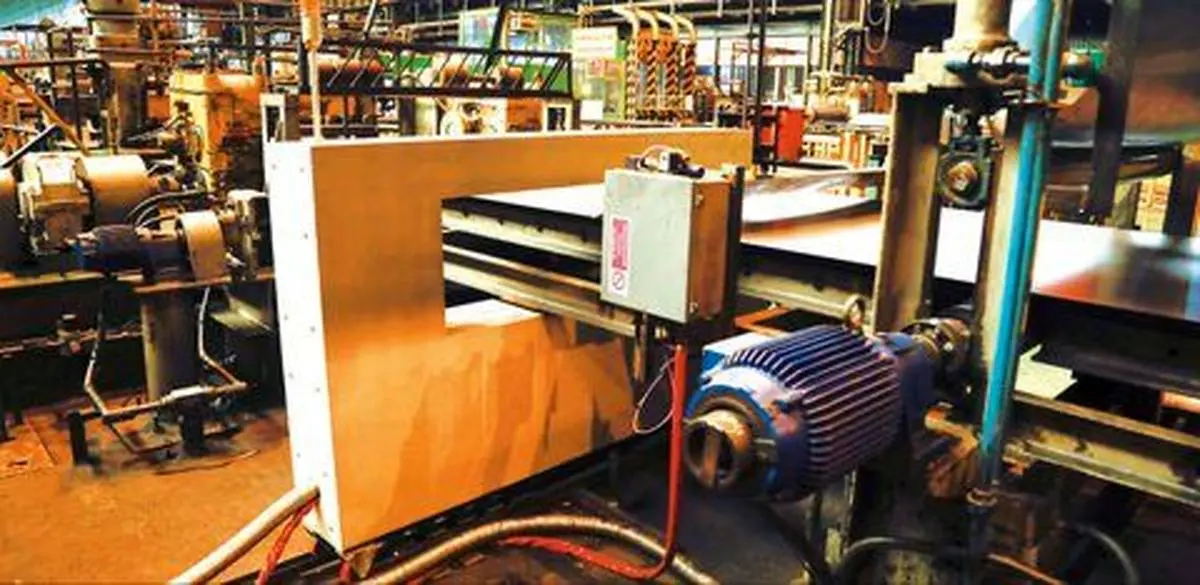
در راستای رفع وابستگی به سازندگان خارجی، بینیازی از واردات و جلوگیری از خروج ارز از کشور، پس از نصب و راهاندازی موفقیتآمیز سیستم ضخامتسنج آنالوگ در واحد اسیدشویی شماره یک، سیستم ضخامتسنج دیجیتال ۷۵-۱۰۰ کیلوولت فولاد مبارکه بومیسازی و با موفقیت در خط تولید واحد کورکتیو ناحیه نورد سرد نصب و راهاندازی شد.
در پی به بار نشستن این موفقیت ارزشمند، مدیران و مسئولان مرتبط با بومیسازی و حوزه بهرهبرداری این تجهیز چنین گفتند:
این پروژه برای اولین بار در کشور اجرا شده و میتوان از آن بهعنوان یک پروژه ارزنده و ویژه ملی نام برد
بهزاد شیرانی، مدیر بازرسی فنی و اتوماسیون فولاد مبارکه اظهار داشت: ازآنجاکه کنترل ضخامت ورق تولیدی از منظر کنترل کیفیت و رضایت مشتری یکی از عوامل بسیار مهم رقابتی به شمار میآید و از دیدگاه اقتصادی نیز بسیار حائز اهمیت است، دستگاههای ضخامتسنج نقش بسیار مهم و حساسی در خط تولید فولاد مبارکه ایفا میکنند؛ بهنحویکه در صورت اختلال در عملکرد آنها، خط تولید با مشکلات و توقفات جدی مواجه میشود.
وی افزود: در فولاد مبارکه ۲۷ دستگاه ضخامتسنج تحت برندهای Measuray، IMS و ITA در نواحی نورد گرم و نورد سرد جهت اندازهگیری و کنترل ضخامت ورق تولیدی در حال کار است. تعداد ۷ دستگاه ضخامتسنج ورق با برند Measuray (ساخت کشور آمریکا) از قدیمیترین سیستمهای نصبشده از زمان راهاندازی فولاد مبارکه بودند که در خطوط مختلف ناحیه نورد سرد به کار گرفته شده بودند؛ اما در طی بیش از ۳۰ سال کار مداوم، دچار استهلاک شدید گردیدهاند و با توجه به عدم تولید اینگونه ضخامتسنجها در کارخانه سازنده و همچنین مشکلات ناشی از تحریمهای خارجی، جایگزینی آنها با سیستم جدیدتر از همان برند و همچنین تأمین قطعات یدکی آنها تقریباً غیرممکن شده؛ بهطوریکه اگر هریک از این سیستمها دچار مشکل شود، عملاً رفع عیب و راهاندازی مجدد آنها به دلایل مذکور ممکن و میسر نیست.
شیرانی گفت: با توجه به مشکلات مذکور، واحد نگهداری و تعمیرات سیستمهای پرتوزا که مسئولیت نگهداری و تعمیرات کلیه کمیتسنجهای پرتویی در فولاد مبارکه را بر عهده دارد، بومیسازی کامل اینگونه تجهیزات و رفع هرچه بیشتر وابستگی به سازندگان خارجی را مطرح کرد. این پروژه برای اولین بار در کشور اجرا شده و با توجه به نیاز سایر صنایع و کارخانجات به اینگونه تجهیزات و حائز اهمیت بودن شرکت فولاد مبارکه و تجارب آن بهعنوان یک شرکت استراتژیک، پیشرو و جهانتراز، میتوان آن را یک پروژه ارزنده و ویژه ملی برشمرد.
مدیر بازرسی فنی و اتوماسیون فولاد مبارکه خاطرنشان کرد: با توجه به مشکلات یادشده، لازم بود این پروژه با همکاری تیمهای مختلف تخصصی از کارشناسان و خبرگان شرکت فولاد مبارکه، شرکتهای دانشبنیان توانمند در این حوزه، اساتید و اعضای هیئتعلمی دانشگاههای مرتبط و همچنین سازمان انرژی اتمی ایران بهعنوان واحد قانونی و متصدی امور مربوط به کاربرد پرتوهای رادیواکتیو در کشور انجام شود.
شناسایی شرکتهای سازنده و دانشبنیان توانمند داخلی یکی از مهمترین اقدامات انجامگرفته
سیامک اورکی، سرپرست واحد سیستمهای پرتوزا تشریح کرد: در تشریح مراحل تشکیل این تیمها و همچنین فعالیتهای صورتگرفته، باید گفت در گام نخست، تحقیق و گردآوری اطلاعات فنی و تخصصی در دستور کار قرار گرفت و در این زمینه اقدامات ذیل انجام شد: تشکیل تیم کارشناسی با حضور کارشناسان و خبرگان اتوماسیون و ابزار دقیق داخلی شرکت، اساتید مجرب و متبحر دانشگاه در زمینه مباحث کنترل و اتوماسیون صنعتی، الکترونیک هستهای، کاربرد پرتوها در صنایع، ایمنی هستهای، استانداردها و الزامات بینالمللی ساخت و تولید جهت انجام تحقیقات فنی و تخصصی در زمینه گردآوری، ساماندهی و طبقهبندی اطلاعات و مشخصات فنی موردنیاز فرایند ساخت سیستمهای ضخامتسنج؛ شناسایی نیازهای فنی و اطلاعاتی خط تولید؛ انطباق آنها با یکدیگر.
وی افزود: نکات فنی بسیار مهم و کلیدی در طراحی و ساخت تجهیزات اندازهگیری و کنترل که با استفاده از پرتوهای رادیواکتیو کار میکنند مطرح است، مانند خطی بودن نتایج اندازهگیری، میزان نشتی پرتو دستگاه و مطابقت با مقادیر استاندارد، رزولوشن، کنتراست، تکرارپذیری و به همین دلیل، انجام پروژه با ارتباط مستمر، هماندیشی مؤثر و اشتراک اطلاعات گروههای مذکور میسر گردید.
سرپرست واحد سیستمهای پرتوزا اظهار کرد: گام دوم شناسایی شرکتهای توانمند داخلی بود. به همین منظور تیم کارشناسی جهت شناسایی شرکتهای دانشبنیان توانمند داخلی با تجربه و روزمه موفق در زمینه طراحی و ساخت تجهیزات الکترونیک، کنترل و اتوماسیون صنعتی تشکیل شد. نکته مهم در این پروسه این بود که اغلب این شرکتها از اطلاعات فنی، توان کارشناسی و توانمندیهای خوبی برخوردار بودند، ولی هیچکدام سابقه طراحی و ساخت اینگونه تجهیزات و مهمتر از آن نصب، راهاندازی و تست در هیچکدام از صنایع مرتبط نداشتند. بدین ترتیب فولاد مبارکه میتوانست یک بستر مناسب با امکانات فنی و تخصصی بسیار ارزشمند جهت بهکارگیری، آزمایش، عیبیابی و در نهایت اجرایی کردن ایدهها و دستاوردهای آنها باشد.
اورکی گفت:در همین راستا، پس از بررسی دقیق سوابق و توانایی شرکتهای مختلف، یک شرکت دانشبنیان توانمند جهت مشارکت در این امر انتخاب گردید. در ادامه، اطلاعات و تجربیاتی که توسط تیم اول گردآوری شده بود در اختیار آنها قرار داده شد و با مشارکت و همکاری کارشناسان داخلی، ساخت قطعات مختلف سختافزاری سیستم شروع و پس از آن نرمافزار مناسب و منطبق بر نیازهای موجود خط تولید، طراحی گردید. پس از مونتاژ بدنه، قطعات، تجهیزات و نصب نرمافزار بهینهسازی شده بهصورت یک ضخامتسنج کامل در آزمایشگاه پرتوزا، این تجهیز بهصورت آزمایشی راهاندازی شد و تحت شرایطی دقیقاً مشابه با سیستم موجود در خط تولید مشغول به فعالیت گردید. در این مدت اشکالات نرمافزاری و سختافزاری با مشارکت و همفکری کارشناسان نگهداری و تعمیرات سیستمهای پرتوزا و کارشناسان تعمیرات اتوماسیون و ابزار دقیق واحد کورکتیو شماره یک شناسایی و رفع گردید.
صرفههای اقتصادی، خودکفایی و عدم وابستگی به تأمینکنندگان خارجی از مهمترین مزیتهای این بومیسازی است
کامران کلوشانی، رئیس واحد کالیبراسیون و ابزار دقیق اظهار داشت: با توجه به اینکه کاربرد پرتوهای رادیواکتیو در صنعت، پس از طی اصول اساسی حفاظت در برابر اشعه شامل توجیهپذیری فعالیت پرتویی، بهینهسازی فعالیت و تعیین و رعایت حدود دُز مجاز فردی، از منظر تأثیر بر سلامت انسانها بسیار حائز اهمیت است و کلیه فعالیتها در این زمینه که طبیعتاً ساخت تجهیزات پرتویی را نیز شامل میشوند، باید مطابق با آخرین استانداردها و الزامات قانونی بینالمللی در زمینه ایمنی هستهای باشد، اخذ تأییدیهها و مجوزهای لازم از واحد قانونی که سازمان انرژی اتمی ایران است بسیار ضروری بود؛ بنابراین طرح این پروژه و توجیه اهمیت زیاد آن در صنایع کشور و جلب رضایت و مشارکت سازمان انرژی اتمی ایران بسیار حائز اهمیت بود.
کلوشانی افزود: پس از رایزنیها و ایجاد کانالهای ارتباطی مؤثر با ریاست سازمان انرژی اتمی و طرح نیازها و احتیاجات صنایع مختلف کشور به ساخت و بهینهسازی کمیتسنجهای پرتویی و ارائه توانمندیهای کارشناسی، زیرساختها و امکانات لازم در پیشرو بودن در طراحی، ساخت، نصب و راهاندازی اینگونه تجهیزات و رفع نیاز داخلی شرکت و همچنین سایر صنایع کشور، نهایتاً منجر به طرح یک تفاهمنامه فیمابین شرکت فولاد مبارکه اصفهان و سازمان انرژی اتمی ایران گردید که پس از تهیه پیشنویس آن و تأیید دو طرف در آینده بسیار نزدیک اجرایی خواهد شد.
رئیس واحد کالیبراسیون و ابزار دقیق تشریح کرد: از دیدگاه فنی و تخصصی، اولین اقدام در این زمینه مشخص کردن پروسه ساخت و انتخاب استاندارد معتبر و بینالمللی ساخت اینگونه تجهیزات و انطباق مشخصات فنی و مراحل ساخت با استاندارد تعیینشده و در نتیجه اخذ مجوز شروع به ساخت سیستم ضخامتسنج بود. یکی از اقدامات بسیار مهم و تخصصی جهت انجام این امر، شبیهسازی سیستم موردنظر جهت مشخص کردن میزان، چگونگی و مسیرهای انتشار پرتو در حین فعالیت دستگاه و میزان نشتی پرتو در نواحی کاری پرتویی شامل ناحیه آزاد، ناحیه تحت کنترل و ناحیه ممنوعه است که این اقدام در قالب یک پروژه جداگانه با همکاری اساتید و اعضای هیئتعلمی دانشگاهی معتبر در این زمینه با استفاده از برنامه شبیهسازی کدهای MCNP طبق آخرین متد شبیهسازی و با نظارت مستمر کارشناسان سازمان انرژی اتمی صورت پذیرفت و موافقت اولیه ساخت ضخامتسنج برای اولین بار در کشور برای شرکت فولاد مبارکه صادر گردید.
مزایای فنی و اقتصادی
از مزایای سیستم ضخامتسنج بومیسازی شده میتوان به نکات زیر اشاره کرد:
استهلاک کمتر نسبت به دستگاه قبلی به علت بهینه شدن سیستم کالیبراسیون دستگاه جدید و تنظیم سطح ولتاژ موردنیاز نسبت به ضخامت ورق تحت پایش و اندازهگیری؛
کاهش زمان توقفات دستگاه؛
تنظیمات امنیتی نرمافزار جهت تعریف سطح دسترسی؛
قابلیت اتصال به PLC؛
قابلیت اعلام خارج از رنج بودن ضخامت ورق بهصورت آلارم صوتی و تصویری و امکان توقف خط در صورت نیاز بهصورت اتوماتیک؛
کاهش زمان توقفات ناشی از نبود قطعات یدکی؛
کامل بودن دانش فنی تعمیرات تخصصی تجهیز و عدم نیاز به کارشناسان خارجی؛
کاهش هزینه چشمگیر بومیسازی نسبت به خرید خارج دستگاه حدود ۷۰ درصد.
با به نتیجه رسیدن این پروژه مهم و باارزش، میتوان به بومیسازی سایر سیستمهای کمیتسنج پرتویی نظیر انواع ضخامتسنج، پوششسنج، غلظتسنج، لولسوئیچ و گیتهای ایمنی کشف مواد پرتوزا با تکیهبر توان فنی و تخصصی کارشناسان و شرکتهای داخلی امیدوار بود و با حمایت مدیریت و مسئولان شرکت فولاد مبارکه، گام بلندی در خودکفایی و عدم وابستگی به تأمینکنندگان خارجی برداشت.
انجام موفقیتآمیز عملیات نصب، تست نهایی و راهاندازی
بهزاد بهادرانی، مدیر ناحیه نورد سرد فولاد مبارکه گفت: پس از انجام تستهای متوالی، رفع اشکالات و موفقیت در آزمونهای اندازهگیری و کنترل و تأیید کارشناسان، سیستم باید در خط تولید و در شرایط کاری قرار میگرفت و جهت حصول اطمینان به کارایی آن در شرایط واقعی تست میگردید. در پی رایزنیهای صورتگرفته با مدیریت محترم نورد سرد، مقرر شد دستگاه ساختهشده بهصورت موازی و در کنار سیستم موجود در خط یک واحد کورکتیو نصب و راهاندازی شود و نتایج اندازهگیری آن همزمان با نتایج سیستم موجود مقایسه گردد.
وی افزود: این موضوع نقش بسیار پررنگ و کلیدی در به ثمر نشستن پروژه داشت، زیرا با توجه به مشکلات و نیاز به توقف خط تولید جهت نصب و راهاندازی و احتمالاً ریسک کاهش تولید، در صورت عدم همکاری مدیریت محترم نورد سرد، پروژه به سرانجام نمیرسید و یا با وقفهای طولانی مواجه میگردید.
بهادرانی بیان کرد: این امر پس از هماهنگی با کارشناسان تولید و تعمیرات اتوماسیون و ابزار دقیق ناحیه مذکور در دیماه ۱۴۰۱ صورت پذیرفت و به مدت چهار ماه، نحوه عملکرد و نتایج آن بهصورت مستمر، تحت پایش و کنترل کارشناسان مربوطه بود و در نهایت پس از رفع اشکالات موجود، صحت عملکرد و نتایج اندازهگیری دستگاه در مقایسه با نمونه مشابه خارجی مستقر در خط، مورد تأیید کارشناسان و مسئولین واحد مذکور قرار گرفت.
شایانذکر است در اواخر فروردینماه ۱۴۰۲ دستگاه خارجی که در کنار دستگاه بومیسازی شده مشغول به کار بود به علت خرابی و عدم امکان تعمیر، از خط تولید حذف گردید و دستگاه جدید بهطور کاملاً مستقل و مطلوب در حال فعالیت است.
بهزاد شیرانی مدیر بازرسی فنی و اتوماسیون فولاد مبارکه در پایان از زحمات کارشناسان و کارکنان واحدهای بازرسی فنی، اتوماسیون و ابزار دقیق، تعمیرات و نگهداری سیستمهای پرتوزا، تعمیرات اتوماسیون و ابزار دقیق ناحیه نورد سرد بهویژه همکاران خط کورکتیو شماره یک، واحدهای بومیسازی، قطعات یدکی، تحقیق و توسعه، ریاست و کارشناسان سازمان انرژی اتمی ایران و همچنین شرکت دانشبنیان فکور پردازش چهلستون و شرکت آرمان پرتو ایدئال که در اجرای این پروژه بسیار مهم و ارزشمند مساعدت نمودند، تشکر کرد.